La metodología Lean -método Lean, Lean manufacturing, Lean enterprise o Lean production– es una modalidad de producción que considera que el gasto en recursos para cualquier objetivo que no sea la creación de valor para el cliente final es un derroche y, por lo tanto, un aspecto a eliminar en cualquier proceso productivo. Bajo la doctrina del pensamiento Lean (Lean Thinking), que se aplica en el ámbito de la industria 4.0, estos «residuos» deben ser identificados, reducidos, o, en la medida de lo posible, suprimidos.
Los tipos de «residuos», según explica el Instituto Lean España, son:
- De transporte (desplazamiento de productos innecesarios).
- De inventario (componentes, trabajo en marcha y productos terminados que no aportan valor).
- De movimiento (desplazamientos innecesarios de personas o equipamiento).
- De tiempos de espera en producción.
- De sobreproducción (por encima de la demanda).
- De defectos (esfuerzo para detectar y solucionar los errores).
Un principio fundamental de la metodología Lean es la fabricación en serie en función de la demanda. En este tipo de modalidad de producción, los productos del inventario solo abandonan cada centro de producción para satisfacer el pedido de un cliente. Los beneficios de esta estrategia son: un ahorro de tiempo, menor inventario, mayor productividad y mejor ratio de eficiencia en el uso de equipamiento.
Mejora continua y objetivos
El concepto Lean se basa en la mejora continua de productos y procesos y, como hemos señalado anteriormente, en la eliminación de actividades que no aportan valor añadido. El concepto de valor añadido es el conjunto de factores o elementos de los productos o tendencias por los que el cliente está dispuesto a pagar una suma adicional de dinero.
La mentalidad productiva de mejora continua es esencial para alcanzar los objetivos de cualquier compañía. Sus principales objetivos son:
- Reducción de defectos y desperdicios.
- Mejora de los tiempos del ciclo productivo.
- Reducción de los niveles de inventario.
- Aumento de la productividad laboral.
- Mejor utilización de la mano de obra y del espacio.
- Mayor flexibilidad.
- Mejora del rendimiento.
Historia de la filosofía Lean
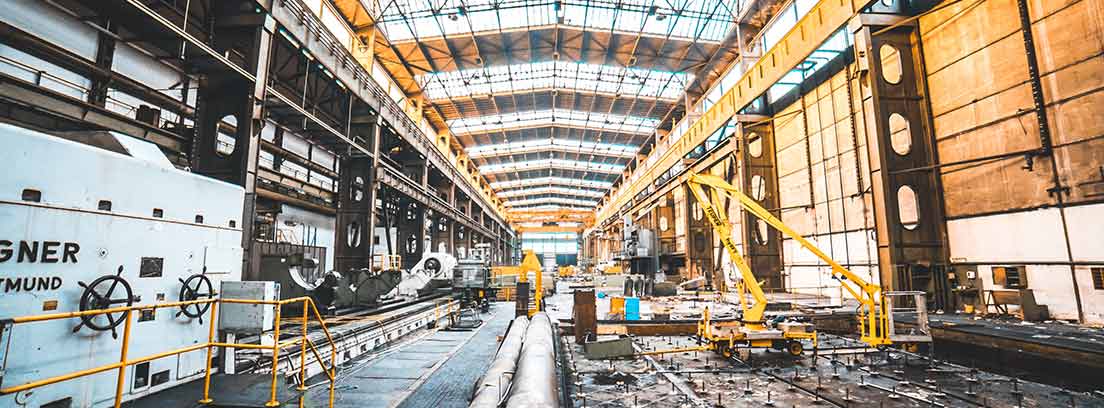
https://bit.ly/38YciBU
Los principios de la filosofía Lean provienen de la industria manufacturera japonesa y de los sistemas de fabricación de Toyota. El término fue acuñado por primera vez, según detalla Businessweek, por John Krafcik en un artículo de otoño de 1988, titulado Triumph of the Lean Production System y publicado en el Sloan Management Review. El término también figura en el libro The Machine That Changed the World, firmado por Jim Womack, Daniel Jones y Daniel Roos.
En estas primeras definiciones, el concepto Lean engloba un conjunto de «herramientas» que ayudan a la identificación y eliminación constante de “residuos” (también denominados como “mudas”). A medida que se eliminan, la calidad de la producción mejora y se reducen tanto el tiempo como los costes de producción. Ejemplos de estas herramientas son:
- Value Stream Mapping (VSM o Mapa de flujo de valor).
- Cinco S (Clasificación, orden, limpieza, estandarización, disciplina).
- Kanban (gestión de tiempos de producción, metodología “pull”).
- Poka-yoke (sistema a prueba de errores).
La visión de Toyota
Existe un segundo enfoque para la filosofía Lean, liderado por Toyota y denominado como Toyota Production System (TPS). La clave de esta visión reside en mejorar el «flujo» del trabajo de forma constante, no eliminando o reduciendo los residuos. La diferencia entre este y el modelo tradicional no es el objetivo en sí mismo, sino más bien el enfoque principal para alcanzarlo.
La ventaja del modelo popularizado por TPS es que arroja una visión holística de todo el sistema productivo, mientras que el modelo clásico de los “residuos” o mudas a veces se centra en aspectos muy particulares. No obstante, ambos están considerados como conjuntos de principios cuyo objetivo es la reducción de costes mediante la eliminación de residuos.
La principal ventaja del modelo TPS es que responde directamente a los problemas que detectaba Toyota en sus propias instalaciones de producción, por lo que está más “pegado al terreno”. En síntesis, esta metodología es el resultado de un aprendizaje impulsado por una necesidad real de mejorar en fábrica, en el que cada paso se ha basado en ideas anteriores y no en algo basado en un marco teórico.
La opinión de Toyota es que el concepto Lean no son las herramientas, sino la reducción de tres tipos de residuos concretos:
- Muda («trabajo sin valor añadido»).
- Muri («sobrecarga del proceso»).
- Mura («desnivel productivo»).